Turkey's custom metal fabrication and stainless steel fabrication service.
We offer a wide range of custom (bespoke) steel fabrication metal services in Turkey.
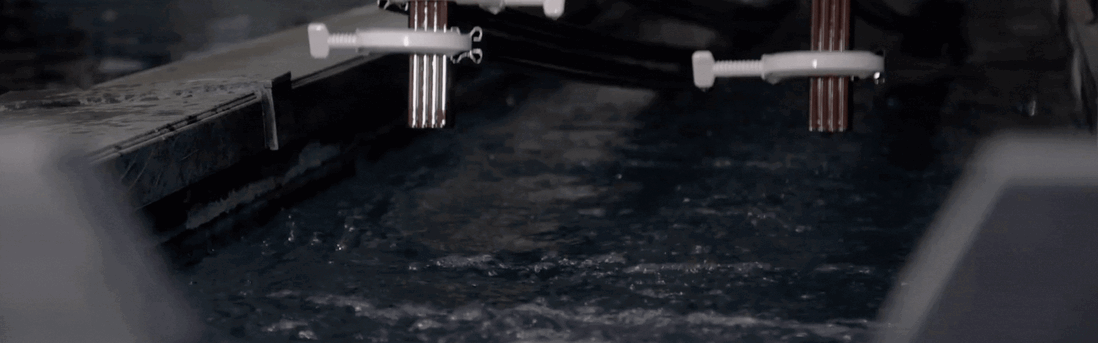
Anodized Coating
Anodizing is a process used to create a protective and
decorative coating on the surfaces of metals. It is a frequently preferred
coating method, especially on metals like aluminum. This process protects by
oxidizing the surfaces of metals, creating an oxide layer.
The anodizing process begins with aluminum or alloy metals
becoming the anode in an oxidation cell in an acid or alkaline-based
electrolyte solution. Based on the principle of electrolysis, this cell
oxidizes the aluminum and forms an oxide layer on its surface. This layer
protects the metal and can also be used for decorative purposes.
There are several different types of anodized coating. These
include sulfuric acid anodizing by electrolysis, chromic acid anodizing, and
hard anodizing. Each method uses different electrolyte solutions and processes
to achieve different properties and thicknesses.
In addition to increasing durability, this coating method
also provides an aesthetic appearance. The oxide layer protects the metal
against scratches, abrasion, and external factors. In addition, this layer,
which can be obtained in different colors, can be used for aesthetic and
decorative purposes.
What Does Anodizing Coating Do?
Since the anodized layer is very hard and thus very
resistant to abrasion, it gives superior properties to aluminum. Since the
anodized coating is resistant to various acids and other chemicals, it protects
aluminum against corrosion in many environments. The transparent structure of
the anodized layer reveals the metallic appearance of aluminum. Thanks to this
feature, various mechanical or chemical processes can be applied to the
aluminum surface that will give it a glossy or matte appearance.
Anodized Coating Process
The anodizing process is a special surface coating process
applied to aluminum. This is accomplished using a mechanical and
electrochemical process. Anodizing increases the durability of aluminum while
providing an aesthetic appearance at the same time.
The anodizing process consists of the following steps:
Preparation: Aluminum parts are cleaned and
degreased. This step ensures the quality and durability of the coating.
Anodization: Aluminum parts are immersed in an
acidic electrolyte solution and subjected to an electric current. In this
process, an oxide layer forms on the aluminum surface.
Painting (optional): Aluminum parts can be
painted after anodizing. This allows the parts to be colored and gives them a
more attractive appearance.
The advantages of anodized coating are:
Durability: Anodizing protects the aluminum
parts’ surface and increases their wear resistance.
Aesthetic appearance: The coating process gives
aluminum parts a more attractive and professional appearance.
Protection: The anodized coating protects
aluminum parts against environmental influences and prevents corrosion.
Color option: In combination with the painting
step, it is possible to obtain different colors with the anodized coating.
Where To Use Anodized Coating
The anodized coating is commonly used in the following
industries:
Automotive Industry: In the automotive industry,
anodized coating is frequently preferred to increase durability and improve the
aesthetic appearance of alloy aluminum parts. In particular, vehicle body
parts, wheels, engine parts, and suspension elements are protected with
anodized coating.
Aerospace Industry: Aluminum and its alloys are
widely used in aerospace due to their lightweight and durability. The anodized
coating is applied to protect these parts against corrosion and improve surface
quality.
Electronics Industry: Parts of electronic
devices, especially portable devices (phones, tablets, laptops, etc.) and
computer cases are protected with anodized coating. Thanks to this coating, the
surface of the parts becomes resistant to scratches.
Construction Industry: Due to the lightness and
durability of aluminum, it is also widely used in the construction industry.
Many structural and decorative aluminum parts, such as door and window
profiles, facade claddings, and stair railings, are protected with anodized
coating.
Industrial Applications: General industrial
equipment, piping systems, tanks, railings, and other metal parts are protected
with an anodized coating to increase durability.
The reason why anodized coating is widely used in these
industries is the need to protect and enhance the advantages offered by
aluminum. This coating method improves aluminum parts’ durability, corrosion
resistance, and aesthetic appearance, ensuring long-lasting use.
Anodised Coating Services: Quality, Reliability,
Reasonable Price
EvoSteel is a leading provider of anodising services in the
industrial sector. Three main reasons for working with us are quality,
reliability and affordability.
Quality
Quality is EvoSteel’s top priority in anodised coating
services. Our team of experts works meticulously to ensure the highest quality
standards for every project. All materials used are carefully selected to
ensure durability and longevity. Anodising is ideal for protecting metal
surfaces and enhancing their aesthetic appearance. This process increases the
metal’s resistance to oxidation and corrosion, making the surface harder and
more durable.
Reliability
EvoSteel has a proven track record of providing timely and
accurate service to our customers. Our commitment to completing your projects
on time and within budget has made us a trusted name in the industry. Customer
satisfaction is our top priority, so we treat every project professionally and
carefully.
Affordable Price
EvoSteel offers quality services at prices to suit every
budget. We aim to offer our customers the best value, which is made possible by
our affordable services. Our anodising services provide a cost-effective
solution while maintaining high-quality standards.
Hard Anodizing Coating
Hard anodizing processes are made for industrial
applications. It is preferred when an extremely hard, friction resistant layer
is desired on aluminum for various engineering applications. Hard anodized
layers can be 25-150 microns thick.
Aluminum Surface Treatment
This is a CR+6 free process designed specifically for
aluminum materials to improve the adhesion of subsequent paint coats. This
knowledge-based process is a material passivation technology with CR+3.
Other Coating Services