Turkey's custom metal fabrication and stainless steel fabrication service.
We offer a wide range of custom (bespoke) steel fabrication metal services in Turkey.
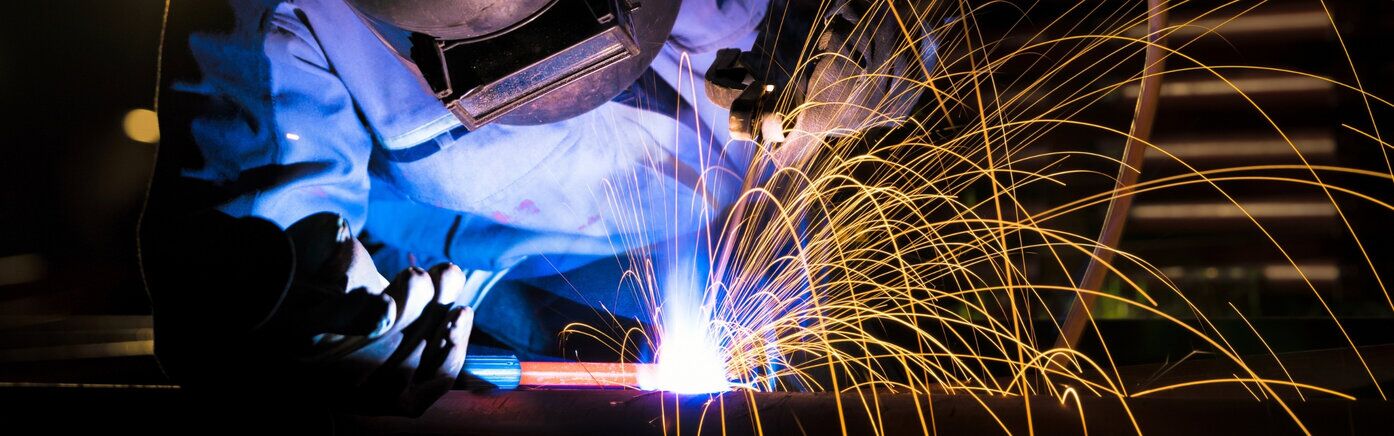
PVD Coating
Physical vapour deposition (PVD) is one of the most
important elements of surface treatment technologies. PVD coating is a
technique used to improve the surface properties of materials. This technique
is widely used by leading companies such as EvoSteel.
PVD coating works by applying a thin film to the surface of
a material. This film layer improves the material’s wear resistance, oxidation
resistance and coefficient of friction. This improves the overall performance
and durability of the material.
The PVD coating process is carried out by concentrating
atoms on the surface of a material. These atoms are vaporised in a vacuum and
condensed onto the material’s surface. This process creates a thin, hard film
layer that bonds tightly to the material’s surface.
How To Make PVD Coating
PVD (Physical Vapour Deposition) coating is a process used
to apply a thin film layer to the surface of a material. The process involves
the following steps:
Vaporisation: The coating material is ionised
and vaporised with high energy. This is usually carried out using a heating
source (laser or electron bombardment system).
Ionisation: The vaporised material is ionised by
plasma created with reactive gases.
Deposition: The ionised material is deposited as
thin film layers on the surface to be coated. This forms a thin and hard film
layer firmly bonded to the material’s surface.
Cooling: After the coating process, the coated
material is cooled.
This process improves the material’s wear resistance,
oxidation resistance and coefficient of friction. This improves the overall
performance and durability of the material.
What Is Pvd Titanium Coating?
PVD (Physical Vapour Deposition) coating provides high
hardness and wear resistance. Here are some features:
High hardness: PVD coating provides a hardness
between 2400-4000 HV. This corresponds to approximately 80-90 HRc.
High wear resistance: PVD coating provides high
resistance to abrasion of materials.
Low coefficient of friction: PVD coating
provides high surface lubricity, which lowers the coefficient of friction.
Chemical resistance: PVD coating provides
resistance to chemical environments.
Low thermal conductivity: PVD coating provides
low thermal conductivity, which helps reduce tool heating.
These properties increase the durability of the PVD coating
and enable it to be used in a wide range of applications. However, how durable
the coating will be for a particular application depends on the coating
material, coating thickness, process parameters and service conditions.
How Long Does PVD Coating Take?
The duration of the PVD (Physical Vapour Deposition) coating
process depends on the material used, coating thickness, process parameters and
many other factors. However, in general, the PVD coating process can take
several hours. This time includes the stages of evaporation, ionisation and
deposition of the material. Each of these processes may require a certain
amount of time, and these times determine the total coating time. Therefore,
more details are needed to determine how long a particular PVD coating process
will take.
Which materials are not suitable for PVD coating?
PVD (Physical Vapour Deposition) coating can be applied to a
wide range of materials, but some materials are less suitable for this process:
High Thermal Conductivity Materials: The PVD
coating process generally requires a temperature below 600°C. Therefore,
materials with high thermal conductivity are less suitable for PVD coating as
they dissipate heat rapidly.
Refractory Metal Carbides and Nitrides: These
materials are difficult to vaporise directly and tend to break down compounds.
Some Tool Steels: PVD coating is particularly
suitable for heat-treated high-speed steel tools. However, some tool steels are
less suitable for this process.
Thick Coatings: PVD coating has a uniform but
slow deposition rate and is unsuitable for coating thicknesses greater than 105
mm.
Therefore, more details are needed to determine whether a
particular material is suitable for PVD coating.
What Is Pvd Titanium Coating?
The coating known as PVD (physical vapor deposition) is
mainly used by our industrialists to protect the material, increase performance
and improve the produced part.
What Does Titanium Coating Do?
- Clean, glossy appearance when applied to a polished surface
- Smooth, matte appearance when applied to a matte surface
- Complex geometric parts can be coated with rotating mechanisms with homogeneous properties.
- It is suitable for small, complex parts such as medical devices, watch parts, micro instruments.
- Due to the thinness of the coating (1-5 µM), dimensional changes are minimal
- It is resistant to damage caused by salt and other corrosive substances.
- It offers a long-lasting, tough exterior that is scratch-resistant. It does not spoil the sharpness of corners and sharp ends.
- The process of applying the PVD coating is completely environmentally friendly.
- Heat treated tool steels can be coated between 180-1600 C and there is no loss of hardness in the parts.
- Very high adhesion forces occur in the coated layers and do not spill from the surface.
- It has a dense crystalline layer structure.
- Tools and dies can be recoated after sharpening.
- Coatings can be removed and re-coated.
Advantages Of Pvd Coating
- Long life
- High rigidity (3500-4000 HV)
- Thin film thickness (1-10 micron standard 2-4 micron)
- Chemical stability (Acid and Corrosion protection)
- low friction coefficient
- Maintaining edge sharpness
- No loss of hardness
- homogeneous coating
- Superior quality
Other Coating Services