Turkey's custom metal fabrication and stainless steel fabrication service.
We offer a wide range of custom (bespoke) steel fabrication metal services in Turkey.
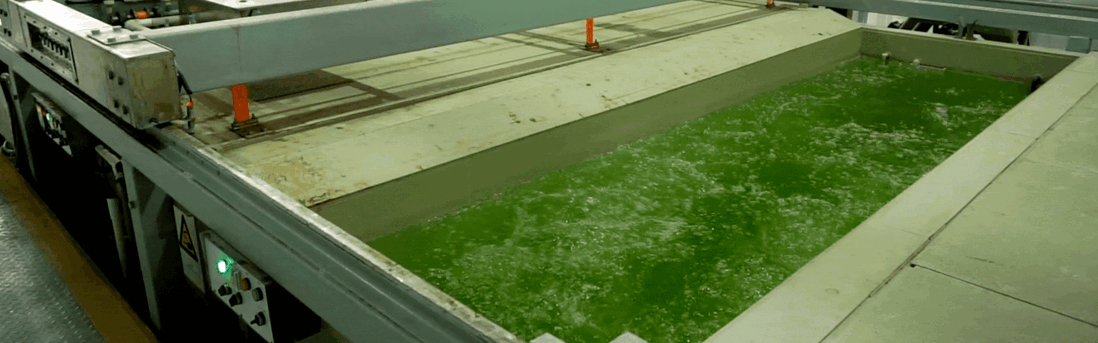
Electroplating
Electroplating is a surface coating technique used in the
manufacturing industry. This method uses electric current to apply a metallic
coating to the surface of a material. Electroplating is an electrochemical
process where the surface of one metal is coated by combining ions of another
metal through an electrochemical reaction.
In recent years, the electroplating process has made
significant advances. These advances have made more accurate and precise
coating processes possible. It has also expanded the coating of different
materials. Now, metallic surfaces, plastics, ceramics, and even composite
materials can be electroplated. This has widened the range of materials and
allowed electroplating to be used in various industries.
What Is Electroplating?
Electroplating is the process of depositing a thin layer of
metal atoms on the surface of a material by electrolysis. In this process, the
added metal called the deposition metal, forms a layer on top of the workpiece,
known as the substrate material. By depositing the desired metal in layers to
improve the physical, mechanical, and chemical properties of the substrate
material, improvements in the material’s properties, such as durability,
thermal and electrical conductivity, wear, and corrosion resistance, can be
achieved.
These enhancements combine various metals to offer
properties better suited to different applications. For example, a steel
material can be electroplated with zinc to improve its corrosion resistance,
making it more durable and long-lasting. Likewise, it is possible to apply
different metals, such as copper plating, to improve the thermal conductivity
of a material’s surface. These methods can be customized according to different
industrial needs, thus ensuring that the material has the desired properties.
How Does the Electroplating Process Work?
Electroplating operates as a process based on the
electrolytic cell principle.
In this process, two metal rods are placed in an
electrolyte. When these rods are connected to opposite battery or power supply
terminals, they act as electrodes with the potential difference created by the
electric current. This current causes the electrolyte solution to dissociate
into metal ions, and positively charged metal ions accumulate on the negative
electrode (cathode).
Positively charged ions are part of the electrolyte, and
their concentration decreases as they accumulate at the cathode. We can create
a source on the anode side by choosing a suitable element to replenish the
concentration of positive ions.
For example, brass is used as a substrate for plating
copper. When connected to the negative terminal, this brass acts as a cathode.
By using an electrolyte, such as copper sulfate solution, we give positive
copper ions due to the breakdown. Copper is used as the anode to replenish the
positive ions of the electrolyte.
In this process, we can vary the process parameters to
control many factors such as plate thickness, metal deposition rate, surface
finish, color, etc. For example, using pure copper sheets provides a more
aesthetic appearance than regular copper rods. With electroplating, the
material can be coated with one or more metals.
Which metals are used in the electroplating process?
The electroplating process allows different coating
combinations to be achieved using various metals. The most commonly preferred
metals for electroplating are:
Copper: Widely used for its conductivity and
resistance to heat. It is also preferred to increase adhesion between
materials.
Zinc: Known for its corrosion resistance. It is
often alloyed with other metals to improve this property further. For example,
zinc-nickel alloys can be resistant to atmospheric corrosion.
Tin: It has good soldering properties and is
environmentally friendly. In addition to being resistant to corrosion, it is
also cost-effective.
Nickel: Wear resistance can be improved by heat
treatment. Its alloys offer different properties and provide resistance,
hardness, and conductivity. It is also resistant to corrosion.
Gold: Known for its high corrosion and wear
resistance. It is also preferred for its conductivity and aesthetic appeal.
Silver: Although not as resistant to corrosion
as gold, it is notable for its ductility and malleability. It has heat and
electrical conductivity.
Palladium: Often preferred over gold or
platinum. Alloyed with nickel, it can offer excellent hardness and plating
quality.
How Electro Galvanized Is Made?
Pre-Process:
The pretreatment process consists of alkaline cleaning, acidic cleaning and electrolytic cleaning steps.
The pretreatment process consists of alkaline cleaning, acidic cleaning and electrolytic cleaning steps.
Covering:
Zinc nickel plating is an electrolytically applied process. The cathode (-pole) is connected to the material to be coated, the anode (+pole) end is connected to the sheet plates used to complete the circuit, and the coating is made under current with rectifiers.
Zinc nickel plating is an electrolytically applied process. The cathode (-pole) is connected to the material to be coated, the anode (+pole) end is connected to the sheet plates used to complete the circuit, and the coating is made under current with rectifiers.
Passivation:
Passivation applied on Zinc Nickel coating can increase corrosion resistance.
Passivation applied on Zinc Nickel coating can increase corrosion resistance.
Top Lacquer:
Different top lacquer applications applied on the coating allow the corrosion resistance to be increased and the friction coefficient to be adjusted depending on the mounting conditions.
Different top lacquer applications applied on the coating allow the corrosion resistance to be increased and the friction coefficient to be adjusted depending on the mounting conditions.
Other Coating Services