Turkey's custom metal fabrication and stainless steel fabrication service.
We offer a wide range of custom (bespoke) steel fabrication metal services in Turkey.
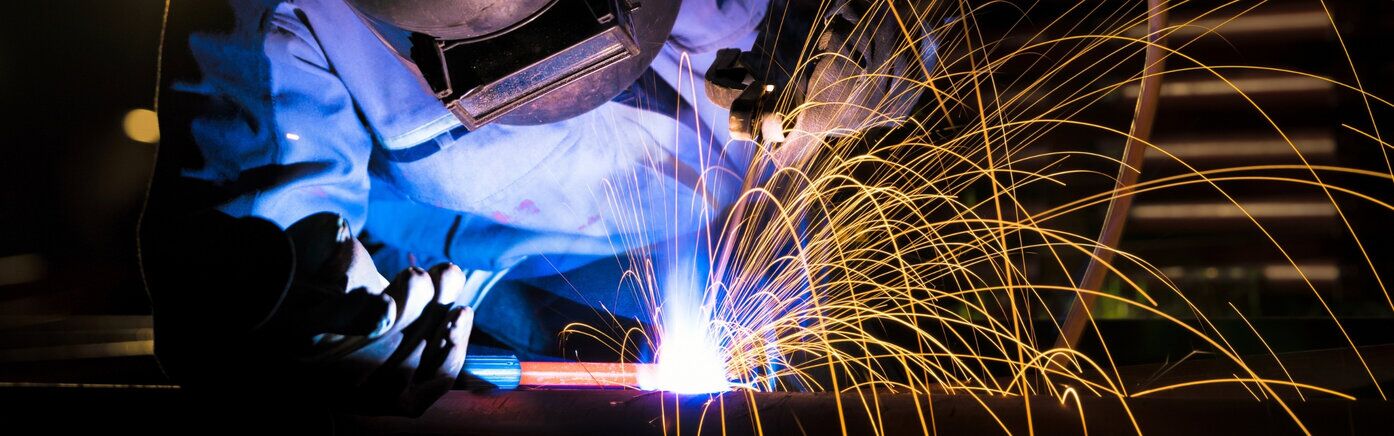
Steel Fabrication
Steel production is one of the cornerstones of the modern world. Steel, obtained by combining iron with carbon, is encountered in almost every aspect of our lives. It is used in a wide range from construction materials to the automotive industry, from kitchenware to heavy industry.
Several basic methods carry out steel production. For example, the basic oxygen furnace (BOF) method involves purifying raw iron by burning it with oxygen. Another method, electric arc furnaces, allows steel to be produced from recycled materials. Each method has advantages and can be preferred according to its intended use.
This production process does not only end with the melting and shaping of the raw material. It involves quality control, adding the right alloys, and forming under different temperatures and pressures. Each is critical to ensure that steel products are durable, flexible and have the desired properties.
The steel industry is also constantly working on sustainability and environmentally friendly production. Efforts in areas such as energy efficiency and waste management are aimed at minimising the impact of steel production on the environment. In other words, steel production is an industrial process and a field that requires constant efforts to reduce its environmental impact.
Steel is a material that has been the backbone of technology from the past to the present. In the future, steel production will gain even more importance with the developments in sustainability and technology.
What Is Steel Fabrication?
Steel production involves the process of taking raw
materials and transforming these materials into a specific shape. The raw
materials are melted and added to the steel before they are formed into a
specific shape. This process involves taking raw materials and turning them
into saleable products. This requires an experienced and skilled technician,
who usually has a very low margin for error. Industrial plants use steelmaking
to produce various products, from auto parts to household appliances.
The main production techniques include cutting, burning,
forming, machining, or welding. Here is an overview of how each of these
techniques works:
Machining: This technique involves shaving
pieces of metal using specialised equipment to shape them into a specific
shape. Tools used in this process include lathes, mills and drills.
Cutting: This involves cutting almost any
material with high precision and without deformation using an abrasive process
called waterjet cutting. You can review the advantages of waterjet cutting
here.
Welding: This is a common form of steel
production. Welding involves bending or joining parts together to make them
into a single piece. Check out this blog post on the differences between MIG
and TIG welding. As a CT welding contractor, we specialise in MIG & TIG
welding of Steel, Stainless Steel and Aluminium. We use Pulse welding machines
to help control the heat applied to a part, minimise deformation and improve
the quality of our parts.
Machinists tasked with steel production are first required
to measure the original shape of the raw material, which may be a flat plate,
reshaped channels, tubes or many other initial forms. Once the steel has been
processed, the next step for the manufacturer requires the shape to be
determined. Two factors determine this outcome: the software package and the
equipment available in the workshop. In this regard, EvoSteel prefers to use
the latest technology to monitor the operation and maintain the efficiency of
the process.
Steel Fabrication in Turkey
Steel Fabrication in Turkey, with our experienced quality
control engineers and team it ensures seamless production in turnkey project
manufacturing services including laser cutting, press brake, welding and
material. We use state-of-the-art CNC Plasma Cutting, CNC Fiber Laser Cutting,
CNC Press Brake, CNC Punch Cutting, Water Jet Cutting, Guillotine Cutting, Saw
Cutting, Tube Pipe Laser Cutting and Sheet Metal Roll Bending benches to
produce black sheet metal, dkp sheet metal, hrp sheet metal, galvanized steel
sheet, spring sheet, brass, titanium sheets and profiles are carefully
processed and shaped.
EvoSteel offers economic solutions in steel production with
its quality service and trust-based cooperation. All of its services are based
on customer satisfaction in accordance with the total quality management
philosophy.
As EvoSteel, we offer a wide range of custom (bespoke) sheet
metal manufacturers, steel fabrication metal services in Turkey. EvoSteel
continues to work with the philosophy of quality for the continuity of customer
satisfaction. It continues to serve you with pleasure and excitement, always
aiming to increase the quality in its sector.
What Are The Basic Raw Materials İnvolved With Metal Fabrication?
There’s quite a few raw materials that are necessary for
metal fabrication. Knowing which items to keep on hand can help speed up the
fabrication process, ensuring that workers always have access to a full supply
of what they need to get the job done. Here are a few basic materials that are
necessary for many metal fabrication projects:
- Plate Metal: fabricators use this to shape the pieces that are working with so that they can have a better range of what they can do.
- Fittings: these are often necessary for creating and completing pieces
- Castings: these are often used to add visual interest to the fabrication. Keeping them on hand may help speed the creation process.
- Formed and Expanded Metal: Expanded metal is grate-like so it is well suited for things like outdoor furniture that need to be able to let moisture flow off.
- Sectional metal: “L” beams are an example of a type of commonly used sectional metal. Z shapes (they resemble the letter Z) are also used as well as bar metal and rod metal
- Flat metal: Flat metal like sheet metal and plate metal are all great for fabrication and can be added to pieces to create visual interest and texture. These are well suited for making shapes as well.
- Welding Wire: Since fabrication requires that metal pieces be welded together, it’s critical to keep various types and thicknesses of welding wire on hand so that pieces can be joined to one another.
Steel & Sheet Metal Manufacturing Company
Steel Fabrication in Turkey, with our experienced quality
control engineers and team it ensures seamless production in turnkey project
manufacturing services including laser cutting, press brake, welding and
material. We use state-of-the-aList of the best steel companies in its area,
offering the best Turkish producers, suppliers and exporters in the steel
industry. As EvoSteel, we are on this list. We are the best and most
competitive steel and stainless steel manufacturer. In this article, we will
talk about the details of steel manufacturing.
Processes
1. CUTTING
1.1 Sheet Metal Cutting
1.1.1. CNC Laser Cutting
In a fiber laser, a cutting process takes place briefly as follows: The laser beams produced in the resonator are carried by fiber cable and transferred to the processing surface perfectly. The cutting process starts when the auxiliary gas used (Oxygen, Nitrogen or Dry Air) and the laser beam contact with the metal surface. With the help of axes with micron precision, the shape of the relevant part is drawn on the machining surface and the cutting process is realized. While these processes are taking place, a perfect automation and perfect cutting parameters are processed in the background.
1.1.2. CNC Plasma Cutting
Plasma cutting is the application of hot and accelerated plasma to the surface to be cut, thanks to a material with high electrical conductivity. With this cutting technique, materials such as aluminum, steel, sheet metal and copper can be cut very sharply and smoothly. Thanks to its high speed, precise cutting and low operating cost, Plasma Cutting Devices have found a place in many areas of the industry from large industrial companies to hobby workshops.
1.1.3. Guillotine Cutting
Guillotine shear service makes many flawless cuts in a short time. It obtains more efficiency from the products with error-free cutting. It is one of the easy and economical ways of rectangular or square cuts of sheet plates. We use CNC automatic guillotine machines for shearing sheet metal.
1.1.4. Punch Cutting
It is a technology that can be an alternative solution tool in cases where cost is more important. It is the process of precisely removing the requested product from the sheet with the help of molds with the help of CNC. In addition, the process of forming sheet material, which cannot be performed with laser cutting technology, but can be done with this technology. Especially, we prefer stainless cuts and perforated cuts to reduce costs.
1.1.5. Water Jet Cutting
Since water jets are cold processing, they do not cause any heat-induced problems (such as burn marks or dark cut edges, flatness and deformation). Another advantage of the water jet is that it can make perfect cuts of sensitive and thick materials that cannot be cut with laser. With the water jet cutting machine, marble, granite, ceramic, laminated glass, stainless steel, aluminum and all hard metals are cut in easily determined dimensions. With this state-of-the-art machine, we can cut even the hardest metals without difficulty or damage.
1.2 Profile Cutting
1.2.1 Saw Cutting
New generation saws are designed to meet all different requirements of customers. These sawing machines allow you to cut many different materials.
1.2.2 Profile and Tube Laser Cutting
Laser cutting offers high precision cutting. Laser cutting machines can not only cut, but also punch and bend holes on the material. For this reason, it increases the production speed significantly. Since lasers provide the possibility of cutting up to 5 axes, shapes that are impossible can be obtained in laser. Profile Cutting, Profile Bending, Profile Drilling.
2. BENDING
2.1 .1 CNC Press Brake Bending
The CNC Press Brake is a sheet metal forming bench that bends the sheet metal raw material into the desired form. With this method, we can precisely bring your materials to the desired form.
2.2 Roll Bending
It is generally used to create cylindrical shapes in sheets.
2.3 Ram Bending
Usually used for bending square pipes.
2.4 Rotary Bending
Used for low tolerance and precise work. It can give the best results in narrow diameter bending applications.
3.WELDING
3.1.1 Gas Metal Arc Welding
The most important advantage of welding made by this method is that the welding place is protected by certain gases during welding and thus it is not affected by air and other factors. Gas welding is the process of making the electric arc between the metal to be welded and a consumed welding electrode part with gas protection. The welding wire, which is applied to the metal to be welded, melts and forms the weld metal. Gas welding is of three types. It is examined as MIG (Metal Inert Gas) and TIG (Tungsten Inert Gas) and MAG (Metal Active Gas). MIG (Metal Inert Gas): The gases used in this welding management are inert gases and are under the protection of Helium and Argon gas. MAG (Metal Active Gas): Gases used in this source are CO2 and mixed gases. Used in steel, low carbon steel or alloy steel. There is no need to change electrodes in MIG and MAG welding as in electric arc welding. The need for electrodes is provided by the welding wire that is continuously driven by the welding machine to the welding area. We can provide services for all your product groups with our certified welders.
3.2 TIG (Argon) Welding
TIG welding is a versatile welding method that can be used for all weldable materials and applications. This method is applied in the production and production of non-ferrous metals that require superior penetration. The main application area is stainless steel, aluminium and nickel alloys. This method is the first choice for applications with high quality expectations.
3.3 Robotic Welding
Robotic Welding ensures the welding quality. Some important points to consider such as suitable wire, correct fixture, compatible gun and consumables in order for the robotic welding machine to provide the most efficient and highest quality welds. With robotic welding, we can weld even the thinnest stainless steel materials with high precision and without deformation.
3.4 Orbital Welding
It is very difficult to reach the highest quality and safety standards using manual welding. Orbital welding provides reliable welding of reproducible quality using a wide range of different techniques. Thanks to its ability to achieve high purity results, orbital welding is used for the semiconductor industry, the production of clean room components, food processing, pharmaceutical, chemical engineering, automotive engineering, biotechnology, power plant construction, shipbuilding and aerospace, for various industries such as pipe and equipment construction that is especially preferred.
4. SURFACE TREATMENT
4.1.1 Sand Blasting
Sandblasting is a method applied to remove oil, dirt, rust and corrosion on the metal due to rust and corrosion over time and extend the life of the metal by coating treatment. The sandblasting process is done with a variety of abrasive materials called specially manufactured grit (gritstone). Sandblasting removes rust and corrosion on the metal surface or micronized dimensions. It is applied before the coating operation significantly increases the coating quality.
4.2 Metallization
It is the application of any metal in wire form to a surface (thermal spray) by turning it into molten and accelerated metal droplets with the help of temperature and pressure and forming a dense protective layer on the surface.
4.3 Coating
4.3.1 Hot-Dip Galvanizing
Hot-dip galvanizing method is the most logical method known to protect steel. The hot dipping method is carried out by immersing and extracting iron or steel into hot pools filled with liquid zinc. As a result of this method, the surface of the metal is covered with an armor that is measured with microns. This armor prevents rusting even in many atmospheric environments. A hot dip applied design can maintain its first day resistance for years without requiring maintenance or repair. With our coating measurement devices, we can control the desired tolerances in all products. We carry out coating processes of all your products in accordance with ISO 1461 and ASTM A123 standards.
4.3.2 Electro Galvanizing
Electro galvanizing is a different process than hot dip galvanizing. The rate of protection of surfaces coated with electro galvanized against impacts is quite high. Resistance to minor scratches on materials coated with this method is quite common. Even against these minor scratches, the material can repair itself and the scratch will disappear. Such protection is not possible in other ways but is possible in combination with electro galvanized coating. Zinc forms a chemical bond with the coated material and forms an alloy on the material surface. This alloy makes the materials more resistant to impacts. We carry out coating processes of all your products in accordance with EN ISO 4042 standards.
4.3.3 Shop Primer
It provides a solid base for the paints to be applied on it due to its very good adhesion property. It is used as a first coat primer to provide high corrosion protection on metal surfaces.
4.3.4 Powder Coating
Electrostatic powder paint, the coated metal surface is baked with a high temperature of 180-200 ° C to cure the paint and thus a painted surface that becomes a part of the metal is eidified. The resulting coating shows excellent resistance to abrasion, corrosion, chemical effects and impacts.
4.3.5 Cataphoresis Coating
It is a wet-applied electrochemical coating method. This method has a resistance against corrosion and impact well above methods such as electrostatic powder paint and electrostatic wet paint. In powder paint and wet paint applications, while painting problems related to part shape are experienced, cataphoresis paint creates the same corrosion resistance on interior and exterior surfaces independent of the part geometry.
5. PACKAGING & LOADING
Packaging is one of the most sensitive points of our company. After manufacturing the product in the best way, it is as important as the quality of manufacturing that your product comes to you in good condition. First, we learn about our customers’ demands and expectations for packaging. In this way, adding our own professionalism, the most suitable way of packing your products is achieved. We have different packaging methods for each product type and shipment type. We do sample packaging work and pack with customer approval. Loading is as important as packaging. We load in the safest and most ergonomic way to prevent damage to the products. Our shipment layout plan is shared by our engineers in 3D.
Quality Control
As EvoSteel, we work meticulously from the beginning to the
end of the production. It is considered as a process that proceeds to
manufacturing with strict inspections and results in the preparation of
comprehensive quality files at the end of the project. Our company, which has
ISO 3834-2 certificate, applies the quality control procedures specified in
these standards for every production as required by the obligation. We not only
adhere to standard quality procedures, but also create specific ITPs
(Inspection Test Plans) for each project, depending on the technical
specifications provided by the customer, even if not requested by the customer,
we prepare a basic quality documentation for each project.
For all raw materials we use in our manufacturing, we
request certificates according to EN 10204 from material suppliers. These
certificates are shared and archived with our customers by project engineers.
The entire quality control process from the receipt of the material to the day
of shipment is carried out and recorded by quality engineers. The most
competent welders are selected in accordance with the specifications of the EN
ISO 9606-1 certificate. We ensure the quality of welded manufacturing by making
the approved manufacturing according to the welding procedure specifications.
Coating activities are also monitored, measured and controlled by certified
quality control engineers.
We can apply any NDT (Non-Destructive Test) tests or other
necessary tests specified in the technical specifications of the project.
Manufacturing traceability is guaranteed by our comprehensive quality control
procedure. All documentation related to manufacturing is stored retrospectively
for 10 years. EvoSteel’s quality system is periodically audited by
internationally accredited certification bodies.
Standards
EvoSteel implements ISO 3834-2: 2005 Requirements in a
disciplined manner with all relevant standards for Welding Quality Assurance in
order to ensure proper product quality and final products to be packaged. Our
resources are carried out by our certified and experienced welders after
preliminary work by our welding engineers who have an international welding
engineering degree. In addition, our quality control team minimizes all errors
that may occur from the beginning of the project to the end. It implements strict
controls in order to ensure the continuous progress of the production within
the tolerances specified in the technical specifications in order to prevent
time loss by providing continuous control during production.
Materials
EvoSteel can use all steels in their manufacturing according
to the customer’s special request.
Mild Steel Grades
SAE1010 (DIN Ck10) (1.1121)
Weld Steel Grades
C10 (1.0301) C15 (1.0401) Ck10 (1.1121)
Structural Steel Grades
St 33 (1.0035), St 37-2 (1.0037), USt 37-2 (1.0036), RSt
37-2 (1.0038), St 37-3 (1.0116),
St 44-2 (1.0044), St 44-3 (1.0114), St 52-3 (1.0507), St
50-2 (1.0050), St 60-2 (1.0060), St 70-2 (1.0070)
Cement Steel Grades
C10 (1.0301), C15 (1.0401) (SAE 1020), 21 NiCrMo 2 (1.6523)
(SAE 8620),
16 MnCrS 5 (1.7139) (SAE 5115), 15 Cr 3 (1.7015) (SAE 5015)
(SAE 4320), 14 NiCr 14 (SAE 3315),
14 NiCr 18 (SAE 3415), 20 CrMo 5 (SAE 4120)
Free Cutting Steel Grades
9 S 20 (1.0711), 9 SMn 28 (1.0715), 9 SMnPb 28 (1.0718), 9
SMn 36 (1.0736), 9 SMnPb 36 (1.0737), 11 SMnPb 30 (1.0718), 11 SMnPb 37
(1.0728), 10 S 20 (1.0721), 10 SPb 20 (1.0722), 35 S 20 (1.0726), 45 S 20
(1.0727), 60 S 20 (1.0728)
Products
As EvoSteel, we can manufacture a wide variety of light,
medium and heavy steel components;
Kiosk, Handrails, Gratings, Stairs, Platforms, Doors,
Cladding Supports, decorative accessories, wall sheet panel, wall sheet metal
panel, electric cabinets, metal cabinets, outdoor cabinets, frames, trailers,
conveyor systems, floor stands, shop stands, market stands etc.
Other Fabrication & Engineering Services